Large and small companies spend large sums of money each year equipping their business units and legal, IT, facilities and security departments to prevent losses. Companies must manage risk to be successful, and the security department plays an integral role in that effort.
One way the security department supports risk management is by properly controlling access to the company's facilities. But access control technology cannot protect the facility by itself. Most facilities have some access points that require only visual badge inspection. A well-designed, quality ID badge goes a long way in supporting a company's desire to mitigate losses. The security badge indicates a great deal about the security department. It reflects the quality of the security program and the level of support the security department receives from upper management. If the badge is not well designed, it is apparent that it is more an instrument of necessity than a part of an orchestrated security program, and this may make the company a target for criminals. A poorly designed badge may also be easy to counterfeit.
Considerations for Strong Badge Design
The employee badge layout must be carefully thought through. You must consider such factors as the location of the company name or logo, the location and orientation of the ID photo, the location of the employee's name, and font and color options. You'll also have to decide what information should be printed on the badge. A combination of text and colors can be used to mark years of service, security clearance, interim clearance, escort privileges, employee numbers, special program access, building access, the badge-issuing site and any personnel information deemed necessary.
Contractors and Visitors
The company must also manage access for contractors and visitors. Badges issued to contractors should be noticeably different from employee badges. Usually the contractor's name and the contract company's name are on the badge. The badge may have "contractor" printed on it. Design distinctions may add to the contractor badge's uniqueness. For instance, if the employee badge is laid out in portrait orientation, the contractor badge may be landscape. Or a contractor badge may be a different color than an employee badge.
By making the badges clearly different, you enable average employees to easily distinguish fellow employees from contractors. They can then support the access control program by recognizing and reporting when a contractor tries to enter an area to which he or she should not have access.
You may decide not to use ID photos on every contractor badge. Often, the length of time the contractor will be on site determines whether his or her badge will include a photo. The longer the stay, the more useful or necessary a photo may be. A list of sites the contractor has access to and an expiration date can be part of the badge.
Visitors also need a badge that provides a unique appearance. The company wants a visitor to have a positive experience during the time spent at its facility, but the visitor's access must be limited to approved locations. Not only are assets at stake, but a visitor can provide feedback to acquaintances that may add to or take away from the company's image. If a visitor's access is not carefully controlled, the company will seem lax in security.
Often a visitor badge resembles a nametag with no photo. A visit date or date range normally appears on the badge as an additional precaution. Temporary visitor badges may be printed on special chemically enhanced papers that begin to display hidden stripes or words, such as "void," after a set period of time, automatically voiding the badge. This ensures the visitor can't reuse the badge after its expiration date. These automatically voiding badges are available with half-day to one-month expiration times.
A visitor's escort should collect the temporary badge as the visitor leaves, but if the badge is not retrieved, there is no significant loss. Since these badges contain no access technology, they aren't expensive. The badge can be printed out at the location where the visitor will gain access to the facility. Some software packages allow the visitor's sponsor to initiate the badge issuing process from the PC in their office and have it automatically print in the lobby or access gate. This approach requires forms and a database that will provide the security department with a history of the visitors at a facility.
Color Consistency
As mentioned, colors may be used to visually categorize badges. But if the color quality is not consistent across the badge printing locations, personnel may have trouble determining the category of a given badge with a quick glance.
One way to address this problem is to select a color standard, such as Pantone. Such standards reference colors more specifically than just "blue" or "red"; they break colors down into percentages of basic primary hues. This ensures greater consistency between badge design and creation programs.
However, consistency problems will still exist at the printing level. Printer ribbons in different printers may output slightly different results, regardless of the consistency of the color ID that is sent to them. Colors will vary slightly between different ribbon or printer manufacturers. The volume that prints at a given printer and the time that elapses between prints will also affect the color. The heat developed during printing will cause the colors to change, so the more badges printed at one time, the more variation you'll see. Standardizing on a given manufacturer can mitigate many of these potential problems. The standard should include model numbers for printers, ribbons, cameras and laminators. Even the color used for the photo background should be specified. Off the shelf software that sends the badging information to the printer can be customized and sent to each badging area. In this way, each badging area software package will properly define colors, mixing of colors and placement of the picture and text on the badge.
Anti-Counterfeiting Measures
No matter how unique your badge designs are, a counterfeiter with the right resources can copy them unless you incorporate visual anti-counterfeit features.
Holograms are common counterfeiting deterrents. They are normally added to the clear overlay placed over the printed badge. A hologram is difficult to duplicate and provides a sophisticated appearance that can add to the company's desired security image. You can buy standardized holograms already on a laminate, or you can have custom holograms, such as your company logo, created for a higher price. Instead of a hologram, the company logo or name can be printed on the clear laminate lightly enough so as not to make the badge information unreadable.
Another variation is using the logo, name or hologram on a tamperproof sticker that can be placed on the badge. There are other anti-counterfeiting measures that require additional equipment to verify a badge's integrity. Ultraviolet printing is one of these. This approach uses an ultraviolet ribbon to print UV-sensitive images or text on the badge. A black light is required to view these elements. Some printers mount both a standard color ribbon and an ultraviolet ribbon. That way the same printer can produce the badge as well as additional ultraviolet protection against counterfeiting.
Another approach is the use of invisible alphanumeric type. The type cannot be viewed except with the use of a laser. These approaches provide a high level of security, but require additional equipment and close inspection of the badges.
You can also add visual anti-counterfeit features into the text of the badge itself. By adding a symbol, microprint or font variations somewhere on the badge, you can make the badge harder to counterfeit without spending extra on special features. A special symbol can be substituted for a letter or number. An older spelling or a word from a different language can be used-substituting bleu for blue, for instance. These more covert approaches are cost effective, but require very close inspection.
Protecting the Badges from Theft
For all these safeguards to be effective against counterfeiting, you must protect the badging stock, technology encoding equipment and badge printing systems. Badging areas should be secured after hours through access control, alarms and CCTV. Password-protect the badge manufacturing software and access control data entry equipment. If the encoding and printing equipment can be password-protected, it should be. The access to software should automatically time out if not in use.
The main supply of badge stock may be stored inside or outside the badging area. At large facilities, several badging areas may coexist, requiring a central badge stock repository. In either case, stock should be under lock and key, with proper accounting procedures for stock that is removed. This includes accounting practices for defective and rejected badges developed during the manufacturing process. This stock must be destroyed and properly documented. Badge stock should not be left in the badging area outside of locked storage. This remaining stock that might be used to counterfeit a badge should be moved to a lockable storage area or to a lockable badge hopper on the printer.
A well-designed badge that is manufactured consistently across the enterprise is a major step in preventing counterfeiting and mitigating a company's losses.
Robert Pearson, PE is a member of the National Standing Committee for ASIS International. He teaches on integrated security systems and corporate security management at The George Washington University in Washington, DC. He is also a consultant for the Strategic Oil Reserve and manager of electronic security systems for Raytheon Co.
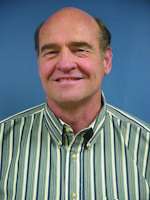
Robert Pearson
Robert Pearson holds a BSEE and is a Registered Professional Engineer. He has been an instructor at George Washington University, teaching “Integrated Security Systems” and “Corporate Security Management.” He has written numerous articles for various technical magazines and has recently published a book, “Electronic Security Systems.” On a day-to-day basis he oversees design, project management, and maintenance of security systems for multiple sites. He is a member of A/E National Standing Council for ASIS International.